Defense Logistics Agency Aviation Operations Center
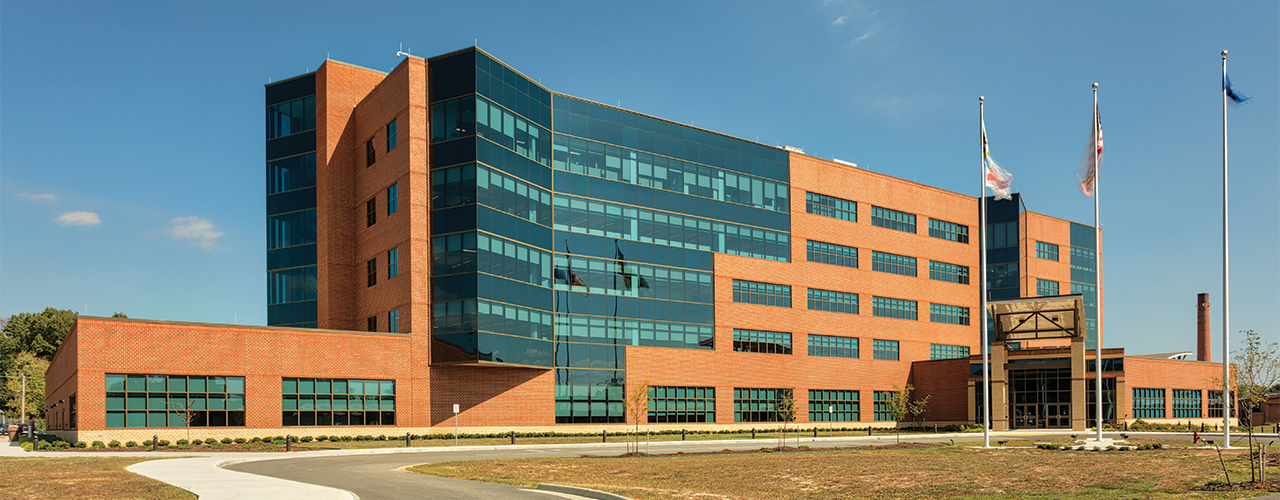
Background
The Defense Logistics Agency Aviation Operations Center provides critical, immediate support for more than 10,000 U.S. military aircraft all over the world, delivering quality parts and services whenever and wherever they are needed.
The new center’s construction at the Defense Supply Center Richmond represents the first of two phases of the project, planning for which began in 2009. Prior to its construction, DLA’s operations, supplies and personnel were spread out at multiple locations, with some utilizing outdated buildings that were erected in the World War II era. Woolpert initiated the final design and construction plans in 2013, with DLA employees from all directorates moving into the phase I facility in 2018.
Challenge
The two-phase project to replace the DLA Ops Center is the largest construction project at the DSCR since WW II. The project involved full and partial demolitions of WW II-era storage facilities and office buildings. Adding complexity to the project, the designs of the phase I and II facilities are much larger than typical government buildings to accommodate thousands of workers and diverse operational needs.
Special foundations were called for because of several impediments presented by the subsurface conditions. Military construction projects are unique in-part because command personnel are often on assignment and do not remain at their posts through the duration of planning, design and execution of the projects.
Solution
Woolpert led a comprehensive architectural and engineering team to complete the design, bidding and construction of the phase I facility. During the planning and design stages for both phases, the team engaged stakeholders from all the directorates that would be relocated to the new facilities.
Through a series of charrettes, the team collected data from and gained insight into the diverse needs of all stakeholders, who in turn gained a sense of ownership and understanding of the project’s scope. The team used BIM to produce the construction drawings, which enabled the stakeholders to virtually walk through the facilities prior to construction.
Outcome
The new phase I facility is a 281,064 square-foot, multistory office building that can accommodate more than 1,600 workers. The building’s HVAC system is an innovative, hybrid geothermal system connected to an energy management system that received a LEED® silver rating.
The building features administrative office areas, reproduction space, multiple unclassified conference and video teleconference spaces, law library, employee support areas as well as storage, equipment and supply rooms. State-of-the-art cybersecurity measures were incorporated. Construction of the phase II facility, which will mirror the phase I facility in size and design, is underway and is slated to be completed by January 2024.
Benefits
The consolidation of DLA’s operations into two facilities located on one secure campus at DSCR provides heightened security and achieves several operational efficiencies in personnel and equipment costs as well as facility maintenance in the long-term. WTS was retained to design and oversee construction of the phase II facility following discussions on lessons learned from the phase I.
Having one comprehensive architectural and engineering team working on the project through its duration provided consistency through leadership changes within the DLA. Employees in the phase I facility, and in the second facility in a few years, can work in a comfortable and modern office environment that is outfitted with the latest in communications and data management technologies. The hybrid geothermal HVAC system helps ensure DLA’s mission readiness and achieves cost efficiencies over time. The fully integrated energy management system utilizes recycled energy and controlled temperatures from the earth through coils that are buried deep in the ground. The geothermal energy system is expected to reduce operational costs by at least 15 percent, which is further boosted by the building envelope itself and other energy efficient electrical, plumbing and wastewater systems.
Client
U.S. Army Corps of Engineers
Location
Defense Supply Center Richmond, VA
Challenge
- Consolidating multiple directorates spread out at various locations into two facilities on one campus
- Design of atypically large government buildings
- Special foundations needed to compensate for less-than-ideal subsurface conditions
- Meeting the demands of U.S. military standards to ensure security and achieve operational efficiencies
Solution
- Conduct planning charrettes
- Develop design drawings
- Perform cost analyses
Services
- Sustainability design
- Construction administration
- Architectural design
- Civil engineering
- Structural engineering
- Mechanical, electrical and plumbing engineering
- Communications engineering
- Post-construction debriefings
Benefits
- Heightened security and sustainability
- Operational efficiencies through consolidation of directorates
- Energy cost savings over time through a geothermal HVAC system integrated with comprehensive energy management
Insights
Blog: Planning, Performing and Persevering: Successfully Tracking a Project Through Multiple Phases